Unlock Precision and Efficiency with Laser Machine Metal Cutting: The Future of Industrial Fabrication
Laser cutting technology has revolutionized the way industries approach metal fabrication, offering unmatched precision, efficiency, and versatility
Laser cutting technology has revolutionized the way industries approach metal fabrication, offering unmatched precision, efficiency, and versatility. Laser machine metal cutting is a non-contact process that uses a focused beam of light to cut through metal with extreme accuracy. This technology has become a cornerstone in manufacturing, automotive, aerospace, and various other sectors, due to its ability to handle both simple and complex designs on a variety of metals.
How Laser Cutting Machines Work
At its core, laser cutting involves focusing a high-powered laser beam on the surface of a metal, where it generates enough heat to melt, burn, or vaporize the material. Here are the key components of the process:
-
Laser Source: The laser is typically generated using either a CO2 (carbon dioxide) or fiber-optic laser, which produces intense energy.
-
Focusing Lens: The laser is then focused through a lens, creating a narrow, intense beam that can precisely cut through materials.
-
Assist Gas: During cutting, an assist gas, typically nitrogen or oxygen, is blown through the nozzle to clear the cutting path and prevent oxidation.
-
Control System: The movement of the laser head is precisely controlled by computer software, allowing for intricate and customized cuts.
Types of Laser Cutting Machines
Laser cutting machines are categorized based on the type of laser they use. Each type is suited for different kinds of materials and cutting applications:
-
CO2 Laser Cutting Machines: These machines use CO2 lasers, which are ideal for cutting thicker materials such as stainless steel, aluminum, and mild steel. They are widely used in industries requiring high precision and speed.
-
Fiber Laser Cutting Machines: Known for their energy efficiency and fast cutting speeds, fiber lasers are effective for thinner metals, and they provide superior cutting quality. Fiber lasers are also more cost-effective than CO2 lasers in the long run due to lower maintenance costs.
-
YAG Laser Cutting Machines: YAG lasers are less common but are used for precision cutting in specific industries like electronics and micro-machining.
Advantages of Laser Machine Metal Cutting
-
Precision and Accuracy: Laser cutting delivers high-precision cuts that can be as small as 0.1mm in diameter. This level of accuracy is crucial in industries where fine details matter.
-
High-Speed Cutting: Laser machines are faster than traditional cutting methods, allowing for quicker turnaround times in production processes.
-
Clean Edges and Minimal Burrs: The heat-affected zone is small, which means the edges of the cut are smooth with minimal burrs, reducing the need for post-processing work.
-
Ability to Cut Complex Shapes: Laser cutting can produce complex shapes and intricate designs with ease, which would be impossible with traditional cutting methods.
-
Reduced Material Waste: The precision of the laser ensures minimal material wastage, making it an eco-friendly and cost-effective cutting method.
-
Non-Contact Process: Since the laser does not physically touch the material, there is no wear and tear on cutting tools, resulting in fewer replacements and maintenance costs.
Applications of Laser Cutting Machines in Metal Processing
Laser cutting technology has a broad range of applications across multiple industries. Here are some of the most common:
-
Automotive: Precision cutting is essential in the automotive industry for components like body panels, exhaust systems, and structural components.
-
Aerospace: The aerospace industry relies on laser cutting for producing complex parts with tight tolerances, especially for lightweight materials like titanium and aluminum.
-
Medical Devices: Laser cutting ensures the high precision needed in the medical device industry for parts such as surgical tools and implants.
-
Manufacturing: From small-scale prototyping to large-scale production, laser cutting is used to create everything from household appliances to industrial machinery parts.
-
Electronics: Laser cutting is used for producing small, intricate parts used in electronics, such as connectors, heatsinks, and circuit boards.
Factors to Consider When Choosing a Laser Cutting Machine
When selecting a laser cutting machine, there are several factors to consider to ensure you make the right choice for your business needs:
Factor | Description |
---|---|
Material Type | Choose a machine based on the types of materials you plan to cut, as different lasers work better with specific metals. |
Cutting Thickness | The thickness of the material you are cutting will determine the type of laser and the power required. |
Cutting Speed | If production speed is crucial, consider machines with faster cutting capabilities, such as fiber lasers. |
Precision Requirements | For intricate designs, high-precision machines are necessary to avoid any defects or errors. |
Budget | Consider both upfront costs and long-term operating costs, including maintenance and energy consumption. |
Key Benefits of Using Laser Cutting Machines in Industrial Applications
1. Reduced Operational Costs
Laser cutting machines are cost-effective in the long run. They require minimal maintenance, and the efficiency of the cutting process ensures faster production times. The reduced waste also contributes to lower material costs.
2. Flexibility in Materials
Laser cutting machines can process a variety of metals, including stainless steel, mild steel, aluminum, brass, and copper. This versatility allows manufacturers to expand their capabilities and take on diverse projects.
3. Automation Potential
Modern laser cutting machines are highly automated and can be integrated with software systems for seamless operation. This integration reduces the need for manual intervention, increasing productivity and decreasing the chance of human error.
4. Environmentally Friendly
Because the laser cutting process is highly efficient, it reduces energy consumption and minimizes material waste. Furthermore, the non-contact nature of laser cutting means there is no use of cutting fluids, making it an eco-friendly option.
FAQ: Laser Cutting Machines for Metal Cutting
Q1: What is the difference between CO2 and fiber laser cutting?
A1: CO2 lasers are typically used for thicker materials and have a longer wavelength, making them better suited for cutting metals like stainless steel. Fiber lasers, on the other hand, are faster and more efficient, especially for thinner materials, and offer lower operating costs.
Q2: How precise is laser cutting?
A2: Laser cutting can achieve extremely high precision, with tolerances as tight as 0.1mm. This makes it ideal for applications requiring detailed, intricate designs.
Q3: Can laser cutting be used for all types of metals?
A3: Yes, laser cutting can be used on a wide range of metals, including stainless steel, aluminum, brass, copper, and even some types of non-metal materials, such as plastics.
Q4: How does the speed of laser cutting compare to traditional cutting methods?
A4: Laser cutting is significantly faster than traditional cutting methods, especially for intricate or detailed cuts. This speed increases productivity and reduces production time.
Q5: Is laser cutting environmentally friendly?
A5: Yes, laser cutting is an environmentally friendly option because it produces minimal waste, requires less energy, and doesn't require cutting fluids, making it a cleaner and more sustainable option than traditional methods.
Q6: Can laser cutting machines be automated?
A6: Yes, many modern laser cutting machines are fully automated and can be integrated with CNC (computer numerical control) systems to streamline production processes.
Laser Cutting: The Future of Metal Fabrication
As industries continue to demand faster, more efficient, and precise fabrication techniques, laser cutting will undoubtedly play an increasingly prominent role in manufacturing processes worldwide. By adopting laser cutting technology, businesses can ensure they remain competitive, meet high-quality standards, and reduce operational costs. With advancements in laser technology, the future of metal cutting looks brighter than ever.
What's Your Reaction?

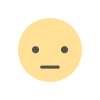
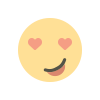

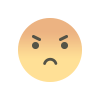

