How to Select the Right Stainless Steel Instrumentation Fittings for Your Application

How to Select the Right Stainless Steel Instrumentation Fittings for Your Application
Choosing the right stainless steel instrumentation fittings is critical for ensuring system efficiency, durability, and safety. Here’s a step-by-step guide to selecting the best fittings for your application.
1. Understand Your Application Requirements
Before selecting fittings, evaluate:
- Operating Pressure & Temperature: Ensure the fittings can handle your system’s pressure and temperature conditions.
- Media Compatibility: Verify that the stainless steel grade is resistant to the fluid or gas being transported.
- Environmental Conditions: Consider exposure to corrosive environments, humidity, and extreme temperatures.
2. Select the Right Stainless Steel Grade
Different grades of stainless steel offer varying levels of corrosion resistance and strength:
- 316 Stainless Steel: Ideal for harsh environments and corrosive applications (e.g., marine, chemical processing).
- 304 Stainless Steel: Suitable for general-purpose applications with moderate corrosion resistance needs.
- Specialty Alloys (e.g., 321, 347): Used for extreme conditions, such as high-temperature or highly acidic environments.
3. Choose the Appropriate Fitting Type
Instrumentation fittings come in different designs to suit various connection requirements:
- Compression Fittings: Easy to install and commonly used in high-pressure systems.
- Pipe Fittings (Threaded or Welded): Provide a secure, leak-tight connection for piping systems.
- Flared Fittings: Used for applications requiring enhanced sealing and vibration resistance.
- Push-to-Connect Fittings: Convenient for quick, tool-free installations in lower-pressure applications.
4. Check for Compliance with Industry Standards
Ensure the fittings meet relevant industry specifications:
- ASME (American Society of Mechanical Engineers)
- ASTM (American Society for Testing and Materials)
- ISO (International Organization for Standardization)
- NACE (National Association of Corrosion Engineers) for oil and gas applications
5. Consider Thread Type and Connection Compatibility
Instrumentation fittings come with different thread types and sealing methods:
- NPT (National Pipe Thread): Tapered threads for tight sealing.
- BSPT/BSPP (British Standard Pipe): Common in European applications.
- Ferrule-based connections: Used in compression fittings for high-integrity seals.
6. Evaluate Pressure Ratings and Leakage Prevention
Ensure the fittings have adequate pressure ratings and consider features like:
- Double Ferrule vs. Single Ferrule: Double ferrule designs offer better grip and sealing.
- Welded vs. Threaded Connections: Welded fittings provide leak-proof reliability, while threaded ones offer easy disassembly.
7. Assess Installation and Maintenance Needs
- Ease of Assembly: Choose fittings that allow quick and secure installation.
- Future Maintenance: Consider fittings that are easy to inspect and replace if necessary.
8. Work with a Trusted Supplier
Selecting a reliable supplier ensures you receive high-quality, certified fittings. Look for:
- Proven track record in the industry.
- Availability of technical support and documentation.
- Options for customization based on your application.
What's Your Reaction?

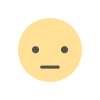
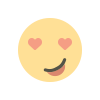

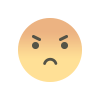

