How Root Cause Analysis Can Transform Risk Management in Refining and Petrochemical Industries
The refining and petrochemical industries operate in high-risk environments where safety, efficiency, and regulatory compliance are critical. Managing risks effectively requires identifying underlying issues that can lead to operational failures, safety hazards, and financial losses. This is where root cause analysis (RCA) plays a vital role. RCA is a systematic approach used to investigate incidents, identify their fundamental causes, and implement corrective actions to prevent recurrence. By integrating RCA into risk management strategies, refining and petrochemical industries can enhance safety, reduce downtime, and improve overall operational efficiency.
Understanding Root Cause Analysis (RCA)
What is Root Cause Analysis?
Root Cause Analysis (RCA) is a structured method used to determine the primary cause of a problem rather than just addressing its symptoms. It focuses on identifying why an issue occurred, enabling organizations to develop effective solutions that prevent similar incidents in the future.
Key RCA Methodologies
Several methodologies are commonly used in RCA to investigate failures and safety incidents:
-
5 Whys Analysis – A simple yet effective technique that involves repeatedly asking "why" until the root cause is identified.
-
Fishbone Diagram (Ishikawa) – A visual representation categorizing potential causes under different factors such as human error, equipment failure, or environmental conditions.
-
Failure Mode and Effects Analysis (FMEA) – A proactive approach to assess potential failure modes, their impact, and corrective actions.
-
Fault Tree Analysis (FTA) – A logical diagram that breaks down possible causes of an incident into hierarchical levels for deeper analysis.
By utilizing these methods, organizations can systematically approach risk management and ensure long-term operational safety.
Common Risks in Refining and Petrochemical Industries
The refining and petrochemical industries face multiple risks that can impact operations, worker safety, and environmental sustainability. Some of the most common risks include:
1. Process Safety Hazards
-
Equipment failures leading to leaks, fires, and explosions.
-
Malfunctions in pressure relief systems causing overpressurization.
-
Corrosion and material degradation affecting pipelines and storage tanks.
2. Operational Risks
-
Human errors in monitoring and controlling refinery processes.
-
Automation and software failures disrupting critical functions.
-
Inefficiencies in maintenance leading to unplanned shutdowns.
3. Environmental Risks
-
Uncontrolled emissions of hazardous gases affecting air quality.
-
Accidental spills contaminating soil and water sources.
-
Regulatory non-compliance resulting in legal and financial penalties.
4. Supply Chain Disruptions
-
Delays in raw material transportation impacting production.
-
Vendor reliability issues causing equipment shortages.
-
Economic and geopolitical factors affecting supply availability.
To mitigate these risks, organizations must adopt a structured approach like RCA to identify root causes and implement corrective measures effectively.
How RCA Improves Risk Management
Root Cause Analysis is an essential component of risk management in refining and petrochemical industries. Implementing RCA provides several benefits, including:
1. Early Detection of Hazards
RCA helps identify potential hazards before they escalate into major incidents. By analyzing minor failures and near-misses, organizations can prevent serious accidents and improve workplace safety.
2. Systematic Problem-Solving
Instead of applying quick fixes, RCA ensures that problems are addressed at their source. This approach reduces recurring failures and enhances long-term reliability.
3. Data-Driven Decision Making
By leveraging historical data and incident reports, RCA enables companies to make informed decisions about safety measures, equipment maintenance, and operational improvements.
4. Regulatory Compliance
Industries must adhere to strict safety and environmental regulations. RCA helps organizations meet compliance requirements by ensuring that risks are thoroughly analyzed and addressed.
5. Cost Reduction
Unplanned shutdowns, equipment failures, and workplace accidents can lead to significant financial losses. RCA minimizes these risks, reducing maintenance costs and improving operational efficiency.
Implementing RCA in Refining and Petrochemical Operations
Integrating RCA into daily operations requires a structured process. Here’s a step-by-step approach:
Step 1: Incident Identification
-
Document all safety incidents, equipment failures, and near-misses.
-
Categorize incidents based on their severity and potential impact.
Step 2: Data Collection
-
Gather detailed information such as equipment logs, operational records, and employee observations.
-
Conduct interviews with personnel involved in the incident.
Step 3: Identifying Root Causes
-
Apply RCA methodologies like the 5 Whys, Fishbone Diagram, or Fault Tree Analysis.
-
Differentiate between direct causes, contributing factors, and root causes.
Step 4: Developing Corrective Actions
-
Implement process improvements, equipment upgrades, or safety training programs.
-
Establish preventive measures to eliminate the possibility of recurrence.
Step 5: Monitoring and Continuous Improvement
-
Regularly review the effectiveness of corrective actions.
-
Update safety protocols based on new findings and industry best practices.
By following this approach, refining and petrochemical industries can strengthen their risk management framework and enhance overall safety.
Challenges and Best Practices in RCA Implementation
While RCA offers significant benefits, implementing it effectively comes with challenges. Organizations must be aware of common obstacles and follow best practices for successful integration.
Common Challenges
-
Resistance to Change – Employees may be hesitant to adopt new investigative procedures.
-
Lack of Training – Ineffective RCA implementation due to insufficient knowledge of methodologies.
-
Data Collection Issues – Incomplete or inaccurate incident reports hindering thorough analysis.
Best Practices for Successful RCA Implementation
-
Establish a Safety Culture – Encourage employees to actively participate in incident reporting and RCA processes.
-
Integrate RCA into Risk Management Frameworks – Align RCA efforts with existing safety and quality improvement initiatives.
-
Leverage Technology – Use digital tools, AI-driven analytics, and automated reporting systems to enhance RCA efficiency.
-
Provide Continuous Training – Equip employees with RCA skills through regular workshops and hands-on exercises.
Bottom Line
Root Cause Analysis is a powerful tool that can transform risk management in the refining and petrochemical industries. By systematically identifying and addressing the underlying causes of failures, organizations can enhance safety, minimize operational risks, and ensure regulatory compliance. Implementing RCA effectively requires a structured approach, commitment from leadership, and a culture of continuous improvement. When applied correctly, RCA not only prevents incidents but also fosters a more resilient and efficient operational environment.
What's Your Reaction?

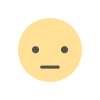
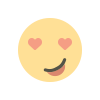

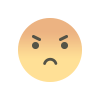

