CNC Turning Tolerances Understanding Precision in Machining
Moreover, understanding and controlling tolerances in CNC Turning contributes to cost efficiency and waste reduction.

CNC Turning is a vital process in modern machining, ensuring the creation of highly accurate and precise components for various industries. This method involves the use of computer numerical control (CNC) lathes to shape metal, plastic, or other materials into desired forms with tight tolerances. The ability to maintain consistency and accuracy in CNC Turning makes it essential for applications in aerospace, automotive, medical, and industrial manufacturing sectors.
Precision in machining is crucial because even the smallest deviation can lead to significant performance issues in mechanical assemblies. CNC Turning enables manufacturers to achieve high levels of accuracy, often within microns, ensuring that parts fit and function perfectly. Understanding tolerances in CNC Turning helps engineers and machinists optimize the production process while minimizing material waste and machining errors.
Understanding CNC Turning Tolerances
Tolerances in CNC Turning refer to the allowable variation in a part’s dimensions from its specified measurements. These tolerances are critical because they determine how well a part will fit and function within an assembly. Engineers define tolerances based on design requirements, with tighter tolerances being necessary for components that demand high precision.
There are three main types of tolerances used in CNC Turning: unilateral, bilateral, and limit tolerances. Unilateral tolerances allow deviation in only one direction from the nominal dimension, while bilateral tolerances permit variation in both directions. Limit tolerances define a range within which the dimension must fall. Each type serves specific purposes depending on the application, material properties, and functional requirements of the component.
Factors Affecting CNC Turning Tolerances
Several factors influence the tolerances achievable in CNC Turning, including material properties, machine capabilities, and cutting tool selection. Different materials have varying degrees of machinability, affecting how precisely they can be turned. Softer materials like aluminum and plastics are easier to machine with tighter tolerances, whereas harder materials such as titanium and stainless steel may require specialized cutting tools and slower speeds to maintain precision.
Machine capabilities also play a significant role in determining achievable tolerances. High-precision CNC lathes with advanced control systems and rigid structures can maintain tighter tolerances compared to older or less sophisticated machines. Additionally, factors such as tool wear, spindle runout, and thermal expansion can impact machining accuracy. Regular maintenance and calibration of CNC equipment help ensure consistent precision over time.
Achieving Optimal CNC Turning Tolerances
To achieve optimal tolerances in CNC Turning, manufacturers employ various strategies such as tool selection, process optimization, and quality control measures. Selecting the appropriate cutting tools and tool holders minimizes vibration and deflection, leading to more accurate machining. Carbide and ceramic inserts are commonly used for their durability and precision-cutting capabilities.
Process optimization techniques, including adjusting cutting speeds, feed rates, and depth of cut, help improve accuracy and surface finish. Implementing real-time monitoring systems and automated feedback loops allows for continuous adjustments during machining, reducing errors and enhancing tolerance control. Quality control measures, such as coordinate measuring machines (CMM) and laser scanning, ensure that finished parts meet the specified tolerances before final assembly.
The Impact of Tolerances on CNC Turning Applications
CNC Turning tolerances directly impact the functionality and performance of finished components. In industries like aerospace and medical device manufacturing, even the slightest deviation can lead to product failure or safety concerns. Maintaining tight tolerances ensures that critical parts, such as turbine blades and surgical instruments, perform reliably under demanding conditions.
Moreover, understanding and controlling tolerances in CNC Turning contributes to cost efficiency and waste reduction. Overly tight tolerances increase production costs due to slower machining speeds, specialized tooling, and extensive quality checks. By balancing precision with practical manufacturing constraints, companies can achieve high-quality results while optimizing production efficiency and profitability.
In conclusion, CNC Turning tolerances are a fundamental aspect of precision machining, influencing the quality, performance, and cost of manufactured components. By understanding the factors affecting tolerances and implementing best practices in machining, manufacturers can produce accurate and reliable parts that meet industry standards and customer expectations.
What's Your Reaction?

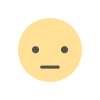
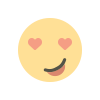

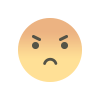

